Are you looking for a reliable Injection Molding ABS supplier in China?
It can be tough to find someone you can trust to deliver strong, long-lasting parts every time.
Don't you want to work with a supplier who makes sure your production runs smoothly without quality issues?
Our article will introduce you to the top 5 Injection Molding ABS suppliers in China who can help you save money without sacrificing quality.
Why choose an Injection Molding ABS company in China?
Significant cost-effectiveness
China has a significant cost advantage in the field of injection molding (especially ABS plastics), mainly due to lower labor costs, large-scale production capacity and a mature supply chain system. This enables Chinese manufacturers to provide high-quality products at more competitive prices.
According to statistics, the average hourly wage of Chinese factory workers is about US$6-8, while the hourly wage of workers in the same industry in the United States is as high as US$15-30, and the labor cost gap is significant. Taking the production of 100,000 ABS plastic shells as an example, the quotation of Chinese manufacturers is usually US$0.5-2/piece, while the unit price of European and American manufacturers may reach US$3-10/piece, and the total cost gap can reach 50%-70%.
Advanced production technology and equipment
China's injection molding companies generally use internationally leading production equipment and technology, including high-precision injection molding machines, automated production lines and intelligent quality inspection systems to ensure high consistency and precision of products.
Industry research shows that the automation rate of China's top injection molding factories exceeds 60%, and some companies have introduced AI visual inspection, and the defect rate can be controlled below 0.1%.
Perfect supply chain and raw material advantages
China is the world's largest producer of ABS plastics, with a complete petrochemical industry chain. Localized raw material supply reduces procurement costs and delivery cycles. In addition, the industrial agglomeration effect (such as the Pearl River Delta and the Yangtze River Delta) enables efficient collaboration in molds, injection molding, post-processing and other links.
China accounts for more than 30% of the global ABS resin production capacity. Major suppliers such as LG Chem (China Factory), CHIMEI, and Formosa all have factories in China, and the raw material procurement cycle is shortened by 1-2 weeks compared to overseas.
Take Shenzhen as an example. The entire process of mold design → injection molding → spraying → assembly can be completed within a radius of 50 kilometers, greatly reducing logistics and time costs.
Rapid response and large-scale delivery capabilities
Chinese manufacturers are flexible in rapid prototyping and mass production, and can adapt to customers' different needs from sample verification to mass production while maintaining a short delivery cycle.
Take Foxconn's injection molding workshop as an example. Its monthly production capacity exceeds 2 million ABS components, which has provided a stable supply for consumer electronics such as Apple headphones.
Rich international experience and compliance
China's leading injection molding companies have long served global customers and are familiar with international quality standards (such as ISO, FDA) and export processes, and can meet the compliance requirements of different markets.
The ocean freight from Ningbo Port to Los Angeles is about 2,000-2,000-4,000/40-foot container, which is 20%-30% lower than European ports (such as Hamburg) and has a shorter voyage.
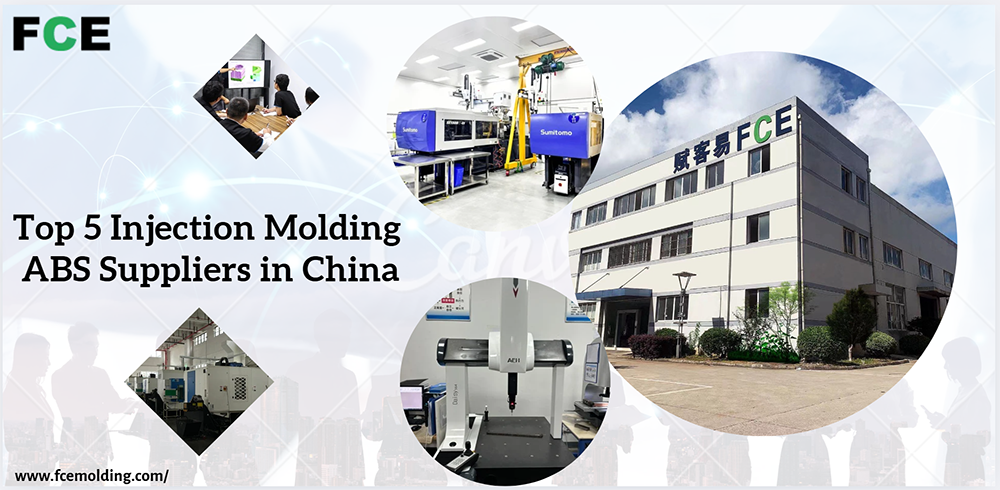
How to choose the right Injection Molding ABS Manufacturers in China?
1. Assess Manufacturing Capabilities
Check if the manufacturer specializes in ABS injection molding and has experience with similar projects.
Evaluate their production capacity, machinery (e.g., hydraulic/electric injection molding machines), and ability to handle your order volume.
Look for quality control measures like ISO 9001 certification and in-house testing facilities.
2. Verify Material Quality & Sourcing
Ensure they use high-grade ABS materials (e.g., from trusted suppliers like LG Chem, Chi Mei, or BASF).
Ask for material certifications (e.g., RoHS, REACH, UL compliance) if required for your industry.
Confirm if they offer custom ABS blends (e.g., flame-retardant, high-impact, or glass-filled ABS).
3. Review Experience & Industry Expertise
Prefer manufacturers with 5+ years of experience in ABS molding, especially in your sector (e.g., automotive, electronics, consumer goods).
Request case studies or client references to verify their track record.
Check if they have expertise in complex geometries, thin-wall molding, or multi-material designs, if needed.
4. Inspect Quality Control & Testing Processes
Ensure they perform strict QC checks (dimensional inspection, tensile testing, impact resistance tests).
Ask about defect rate and how they handle quality issues (e.g., replacement policies).
Look for third-party inspection options (e.g., SGS, BV) for added reliability.
5. Compare Pricing & Payment Terms
Request detailed quotes from 3–5 suppliers to compare costs (mold tooling, per-unit price, MOQ).
Avoid unusually low prices, which may indicate subpar materials or shortcuts.
Negotiate flexible payment terms (e.g., 30% deposit, 70% before shipment).
6. Check Logistics & After-Sales Support
Confirm their shipping options (air, sea, DDP/DAP) and ability to handle export documentation.
Ask about warranty policies and post-production support (e.g., mold maintenance, reorders).
Ensure they work with reliable freight forwarders for timely delivery.
7. Visit the Factory or Audit Virtually
If possible, conduct an on-site audit to verify facilities, cleanliness, and workflow.
Alternatively, request a virtual factory tour or live video inspection.
Look for automation levels—modern factories reduce human error.
List of Injection Molding ABS Companies in China
Suzhou FCE Precision Electronics Co., Ltd.
Company Overview
With over 15 years of industry expertise, FCE specializes in high-precision injection molding and sheet metal fabrication, serving as a trusted partner for OEMs and global brands. Our core capabilities extend to end-to-end contract manufacturing, catering to diverse industries including packaging, consumer appliances, home automation, and the automotive sectors.
In addition to traditional manufacturing, we offer silicone production and advanced 3D printing/rapid prototyping services, ensuring a seamless transition from concept to mass production.
Backed by a highly skilled engineering team and rigorous project management, we deliver precision-engineered solutions with a focus on quality, efficiency, and scalability. From design optimization to final production, FCE is committed to turning your vision into reality with unmatched technical support and manufacturing excellence.
Industry-Leading Injection Molding Services
Cutting-edge technologies and continuous investment in advanced manufacturing.
Expertise in in-mold labeling & decoration, multi-K injection molding, sheet metal processing, and custom machining.
Highly Experienced Professional Team
Engineering & Technical Experts:
5/10+ team members with over 10 years of design & technical experience.
Provide cost-saving & reliability-focused suggestions from the initial design stage.
Skilled Project Managers:
4/12+ team members with over 11 years of project management experience.
APQP-trained & PMI-certified for structured project execution.
Quality Assurance Specialists:
3/6+ team members with over 6 years of QA experience.
1/6 team member is a Six Sigma Black Belt certified professional.
Rigorous Quality Control & Precision Manufacturing
High-precision inspection equipment (OMM/CMM machines) for full-process quality monitoring.
Strict adherence to PPAP (Production Part Approval Process) is required to ensure a smooth transition to mass production.
Lomold Moulding Technology Co., Ltd.
Specializes in high-precision ABS injection molding, offering services from prototyping to mass production for automotive, electronics, and consumer goods.
Firstmold Composite Engineering Co., Ltd.
Focuses on ABS plastic molding with advanced techniques like in-mold labeling, multi-material molding, and tight-tolerance manufacturing for industrial and medical applications.
HASCO Precision Mould (Shenzhen) Co., Ltd.
A well-known supplier of ABS injection-molded components, particularly for automotive, home appliances, and electrical enclosures.
Tederic Machinery Co., Ltd.
Provides custom ABS injection molding solutions, specializing in high-performance plastic parts for medical, packaging, and industrial equipment.
Buy Injection Molding ABS directly from China
Injection Molding ABS Product Testing from Suzhou FCE Precision Electronics
1. Raw material testing (Pre-Molding)
Melt flow index test (MFI)
Test the melt fluidity of ABS particles to ensure that it meets the requirements of the injection molding process.
Thermal analysis (DSC/TGA)
Verify the thermal stability and glass transition temperature (Tg) of the material through differential scanning calorimetry (DSC) and thermogravimetric analysis (TGA).
Moisture content test
Avoid moisture in the raw materials, which may cause bubbles or silver streaks in the injection molded parts.
2. Injection molding process monitoring (In-Process)
Process parameter recording
Monitor key parameters such as barrel temperature, injection pressure, and holding time to ensure consistency.
First article inspection (FAI)
Quickly check the size and appearance of the first batch of molded parts, and adjust the mold or process.
3. Finished product performance test (Post-Molding)
A. Mechanical performance test
Tensile/bending test (ASTM D638/D790)
Measure mechanical indicators such as tensile strength and elastic modulus.
Impact test (Izod/Charpy, ASTM D256)
Evaluate the impact toughness of ABS (especially in a low temperature environment).
Hardness test (Rockwell hardness tester, ASTM D785)
B. Dimension and appearance inspection
Coordinate measurement (CMM)
Inspect key dimensional tolerances (such as hole diameter, wall thickness).
Optical microscope/two-dimensional imager
Inspect surface defects (flash, shrinkage, weld line, etc.).
Colorimeter
Verify color consistency (ΔE value).
C. Environmental reliability test
High and low temperature cycle (-40℃~85℃)
Simulate dimensional stability in extreme environments.
Chemical resistance test
Immerse in media such as grease, alcohol, etc., and observe corrosion or swelling.
UV aging test (if outdoor use is required)
4. Functional verification (Application-Specific)
Assembly test
Check the compatibility with other components (such as snap-on, threaded fit).
Flame retardant test (UL94 standard)
Applicable to electronic and electrical products.
Air tightness/waterproof test (such as automotive parts)
5. Mass production quality control
PPAP document submission (including MSA, CPK analysis)
Ensure mass production process capability (CPK≥1.33).
Batch sampling inspection (AQL standard)
Random sampling inspection according to ISO 2859-1.
Purchase Injection Molding ABS Directly from Suzhou FCE Precision Electronics
If you are interested in ordering Injection Molding ABS technology from Suzhou FCE Precision Electronics, we are always ready to help you.
Please feel free to contact our sales team through the following channels:
Email: sky@fce-sz.com
Our professional team is prepared to answer your inquiries, provide detailed product information, and guide you through the purchasing process.
We look forward to the opportunity to collaborate with you. To provide additional useful information:
You can find further information about our products and services by visiting our official website: https://www.fcemolding.com/
Conclusion
China is home to some of the world’s leading ABS injection molding suppliers, offering high-quality materials, precision manufacturing, and cost-effective solutions. As a trusted provider in this industry, FCE is committed to delivering superior ABS injection molding services tailored to your specific needs.
With advanced production technology, strict quality control, and a customer-focused approach, we ensure durable, high-performance ABS components for various applications—from automotive and electronics to consumer goods. Our competitive pricing, fast turnaround times, and reliable supply chain make us the ideal partner for your project.
Post time: Apr-29-2025